The story of the Fonderia Artistica Marinelli spans many years, built on ancient expertise and family traditions, where art and the highest Florentine craftsmanship merge to create one-of-a-kind works to admire and collect.We spoke with its owner, Ferdinando Marinelli – grandson and namesake of the historic founder – to learn more about the foundry’s work, which still relies today on the fascinating 16th century technique of lost-wax bronze casting.
What is an artistic foundry and how does it work?
At the Fonderia Artistica Marinelli, bronze sculptures are produced either from other sculptors’ designs or casts of existing artworks. These can be monuments, furnishings, or scaled-down reproductions, all carried out with skill and expertise by the factory’s master artisans.
“In the early 1900s, when the Fonderia was established”, Ferdinando Marinelli told us, “the lost-wax casting techniques were still the same as those used in the Renaissance”. Over time, production methods have evolved, but the Florentine foundry chose to keep the traditional approach, “because trials with faster modern techniques have resulted in a much lower artistic quality”.
It is precisely this excellent artistic quality that enabled the Fondazione Marinelli to gain international recognition and secure prestigious commissions from around the world.
Are you interested in articles like this?
Sign up for the newsletter to receive updates and insights from BeCulture!
An exceptional portfolio, between past and present
It’s hard to say which of the many works created makes Marinelli most proud, because each has something special about it – some even come with anecdotes that have become legendary over the years. One such example is the set of seven bronze horses made in 2001 for the Denver Broncos Stadium in Colorado, USA. This imposing group of sculptures was commissioned by the stadium’s owner, Patrick Bowlen, to celebrate the famous American football team, whose symbol is a horse. When the time came to move the bronze sculptures out of the Fonderia, they turned out to be too large to fit through. Marinelli and his collaborators realized a drastic step was necessary and ended up demolishing part of the building. “Knocking down the lintel of the door at the fonderia in Rifredi gave us the opportunity to build a new foundry in Barberino Val d’Elsa (Florence), bigger and better equipped”, the owner revealed.
Years earlier, a similar challenge arose when transporting an equestrian monument bound for the Arlington Memorial Bridge in Washington, USA, to the port of Livorno: “That time, the ATAF Tramway Company had to dismantle much of its overhead lines along the roads used by the crate containing the artwork”, Marinelli recalled.
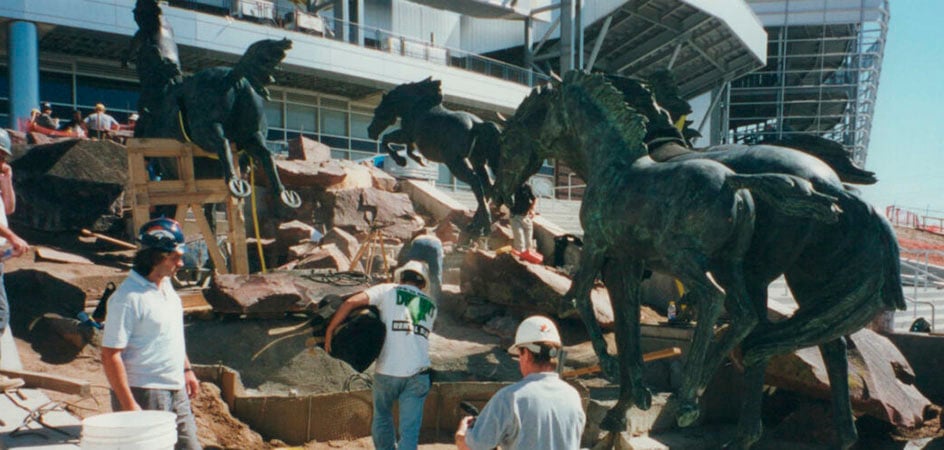
But it wasn’t just the United States that embraced and valued Fonderia’s work. Even before that, the Santa Sede turned to Florentine technical and artistic expertise for the monumental ramp of the Vatican Museums (designed by the sculptor Antonio Maraini) and the Porta Santa of the Basilica di San Pietro (modeled by the Sienese artist Vico Consorti, replacing the previous wooden one), to name just a couple of examples. Then came Russia, which in 1998 commissioned the restoration of the decorations of two halls in the Kremlin, destroyed under Stalin’s administration; the urban redevelopment project in Skopje, the capital of North Macedonia, involving the creation of the city’s most important monuments; and so on to the present day.
This intense activity has not prevented the Fonderia from also engaging with the great masters, reproducing timeless masterpieces of Italian art thanks, in part, to the extensive collection of plaster casts preserved to this day.
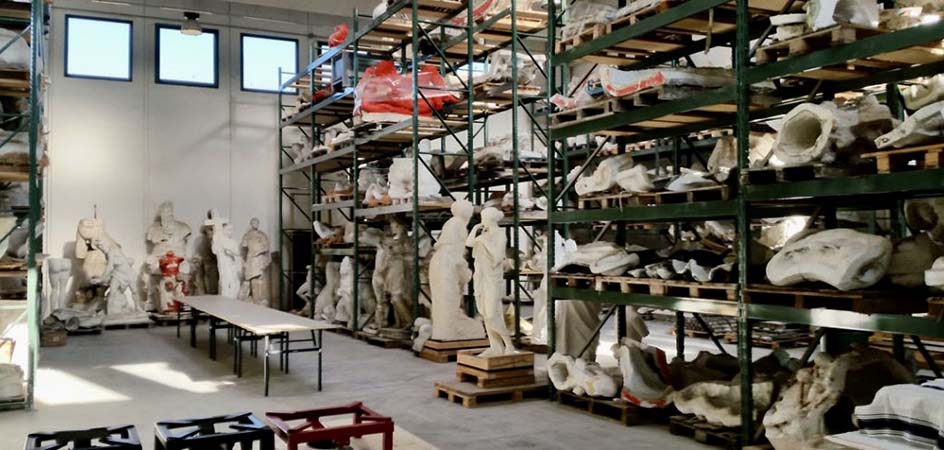
An incredible family legacy
“The casts made by Ferdinando Marinelli Sr. and passed down to Ferdinando Marinelli Jr. number around 750, both large and small”. It’s an enormous archive and an amazing family inheritance, demonstrating the founder’s – and subsequent generations’ – dedication to classic and Renaissance art, an invaluable heritage of beauty and artistic talent.
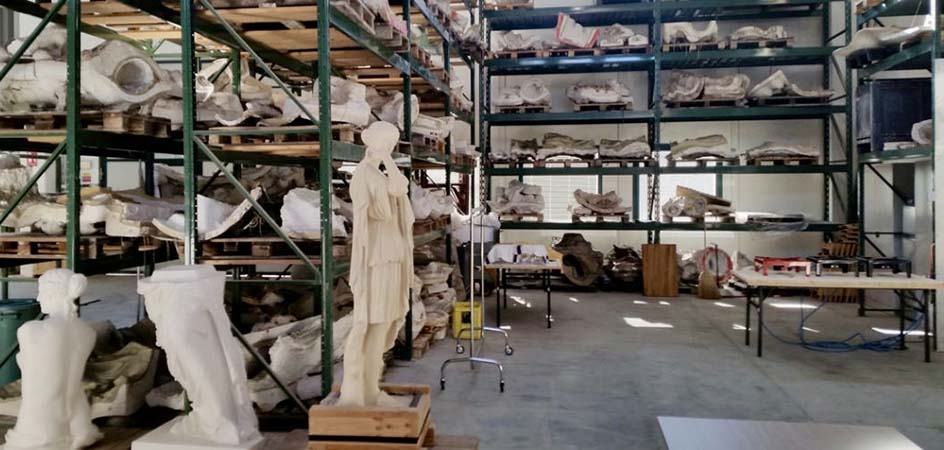
The gipsoteca (plaster-cast gallery) is precisely what allows the Fonderia to recreate bronzes identical to the originals.
A few examples include the life-size bronze casting of the David by Michelangelo, the replicas of the Porcellino of Florence and the Chimera of Arezzo, the David by Donatello, and the list goes on. Alongside these, smaller-scale productions are no less labor-intensive or meticulously executed.
Whether colossal or more modest in size, the sculptures are still cast today using the ancient lost-wax method, the same technique used back in 1588 in the workshop the Medici established for Giambologna, passed down from artisan to artisan, right up to the present.
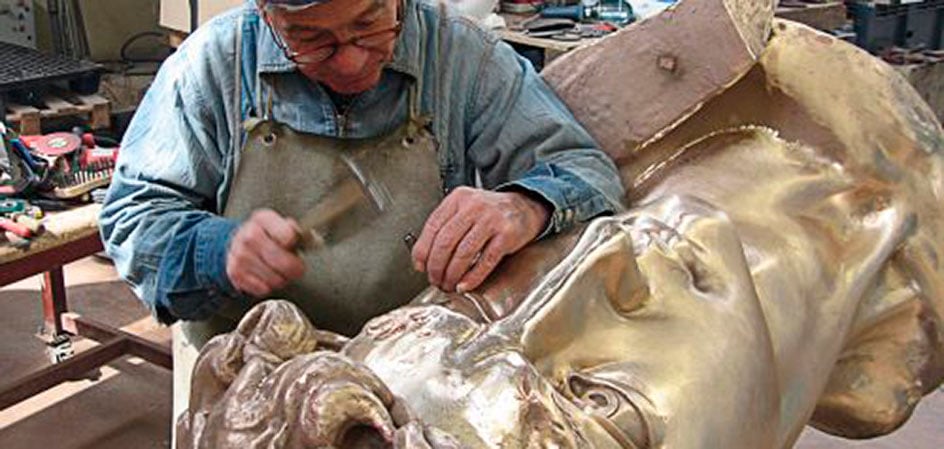
Lost-wax casting: a centuries-old technique that still works today
Entirely performed by hand, lost-wax casting requires experience, precision, and patience – the very qualities the Fonderia Marinelli’s artisans possess and exercise daily. These skills are crucial, “because they can work exactly as the ancient and Renaissance artists did. And we’re proud of that”.
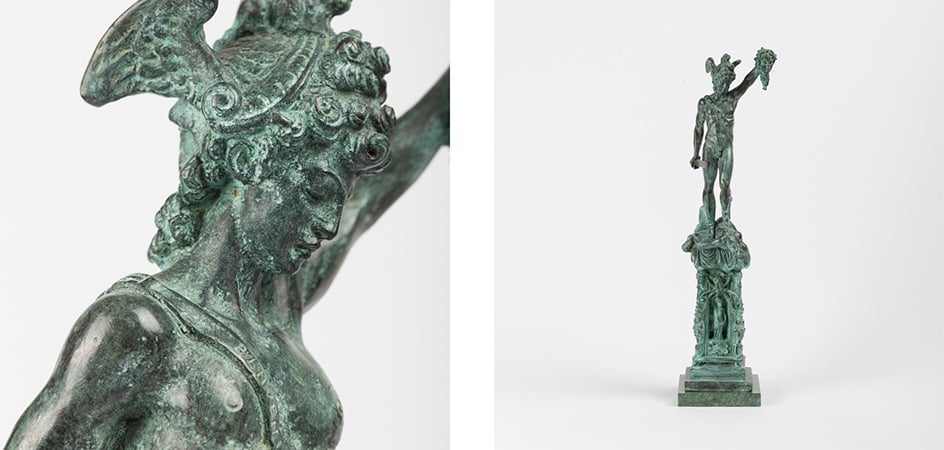
The phases are long and delicate. It begins with creating a wax model, which will match the thickness of the final bronze sculpture. This model is then covered with a refractory material (loto, composed of crushed stone and plaster), used inside as well to fill it. A complex arrangement of tubes ensures that in the following stages, bronze can reach every area of the mold, replacing the wax.
Next comes the firing process: during firing, the refractory material solidifies and the wax melts away, leaving a negative impression of the work. The molds are then buried in moist earth so the liquid metal doesn’t deform them. In the space left by the wax, a bronze alloy is poured in. The tubes – still in place – allow air and the gases produced to escape. Once unearthed and the mold (or molds, for larger works) is broken, what emerges is the so-called rough casting, still far from the finished piece.
At this point, the tubes need to be removed, followed by sandblasting and chiseling – a painstaking process that only highly qualified artisans can carry out with excellent results. Finally, the patina is applied to give the piece the desired level of oxidation.
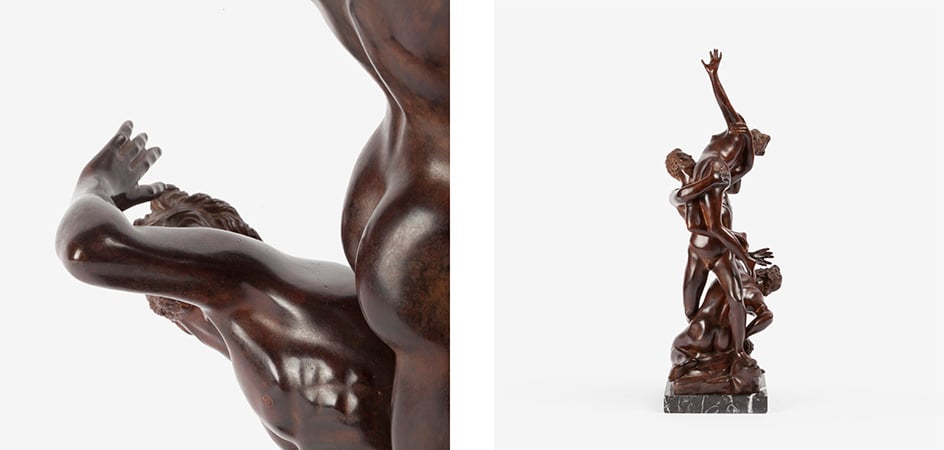
Time, along with specialized labor, is therefore one of the biggest factors affecting production. “To create the David by Michelangelo in its original size out of bronze usually takes about a year”, Marinelli points out.
That’s why every work produced at the Fonderia is a true masterpiece of technique and skill, offering tangible proof of the remarkable standards this workshop has achieved.
Florentine high craftsmanship has a glorious past and an equally bright future, and we are honored to help support it.